دستگاه تصفیه آب
دستگاه تصفیه آب کشاورزی
دستگاه تصفیه آب دامداری
دستگاه تصفیه آب صنعتی
تصفیه آب صنعتی 500 مترمکعب
تصفیه آب صنعتی 400 مترمکعب
تصفیه آب صنعتی 300 مترمکعب
تصفیه آب صنعتی 250 مترمکعب
تصفیه آب صنعتی 200 مترمکعب
تصفیه آب صنعتی 150 مترمکعب
تصفیه آب صنعتی 100 مترمکعب
تصفیه آب صنعتی 75 مترمکعب
تصفیه آب صنعتی 50 مترمکعب
تصفیه آب صنعتی 25 مترمکعب
تصفیه آب صنعتی 20 مترمکعب
تصفیه آب صنعتی 15 مترمکعب
تصفیه آب صنعتی 10 مترمکعب
تصفیه آب صنعتی 5 مترمکعب
دستگاه تصفیه آب نیمه صنعتی
دستگاه تصفیه آب خانگی
مخزن آب
مواد شیمیایی
الکتروپمپ
ضدعفونی آب با اشعه UV
دستگاه سختی گیر رزینی
قطعات آب شیرین کن صنعتی و خانگی
کف کش و شناور
تجهیزات کنترل
- محصولات برنجی
مخازن تحت فشار: بررسی و کاربردها
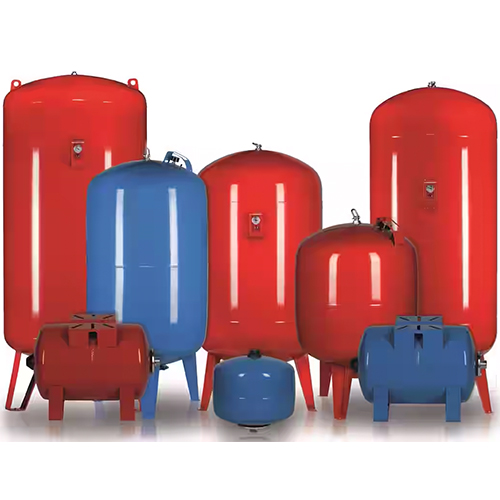
مخازن تحت فشار: بررسی و کاربردها
مقدمه
مخازن تحت فشار، تجهیزاتی هستند که برای ذخیره و انتقال سیالات تحت فشار بالا طراحی شدهاند. این مخازن در صنایع مختلف، از جمله پتروشیمی، انرژی، و آب و فاضلاب کاربرد دارند. اهمیت مخازن تحت فشار در صنایع امروزی به دلیل نیاز به ذخیرهسازی امن و انتقال سیالات با فشار بالا بسیار زیاد است.
برای مثال، در صنایع نفت و گاز، ذخیره و انتقال گازهای فشرده برای تولید و مصرف انرژی از مهمترین موارد کاربرد این مخازن است. همچنین در صنایع پتروشیمی، نگهداری مواد شیمیایی که در فشارهای بالا واکنشپذیری دارند، نیازمند مخازن با استانداردهای ایمنی دقیق است. در این مقاله، به بررسی انواع مخازن تحت فشار، طراحی و ساخت آنها، نکات ایمنی مرتبط و کاربردهای متنوع این نوع مخازن میپردازیم.
انواع مخازن تحت فشار
مخازن تحت فشار به چند دسته کلی تقسیم میشوند که هر کدام خصوصیات فنی و کاربردی متفاوتی دارند.
1- مخازن عمودی
این مخازن به صورت عمودی نصب میشوند و معمولاً برای ذخیره سیالات در مقادیر زیاد طراحی شدهاند. ساختار آنها به گونهای است که فشار داخلی به طور یکنواخت به دیوارهای مخزن وارد میشود و مقاومت خوبی در برابر نیروهای عمودی دارند.
مزایا:
اشغال فضای کمتر نسبت به مخازن افقی
سهولت در کنترل و مشاهده سطح سیال
مناسب برای ذخیره سیالات مایع و گازهای فشرده
2- مخازن افقی
این نوع مخازن به صورت افقی قرار دارند و بیشتر برای سیالاتی با ویسکوزیته بالا یا کاربردهای خاص استفاده میشوند. مخازن افقی به دلیل توزیع فشار متفاوت در اثر وزن و فشار داخلی، نیازمند طراحی خاصی هستند تا از شکست یا خمش دیوارهها جلوگیری شود.
مزایا:
مناسب برای سیالات سنگین با فشار بالا
سهولت در نصب در فضاهای محدود عرضی
امکان استفاده در صنایع غذایی و دارویی
3- مخازن دوجداره
این مخازن به گونهای طراحی شدهاند که در صورت نشتی، مایع در بین دو جداره محبوس میشود و به این ترتیب از آلودگی محیط زیست جلوگیری میشود. این نوع مخازن برای نگهداری مواد خطرناک یا سمی کاربرد فراوانی دارند.
ویژگیها:
وجود دو لایه مستقل با فضای خالی برای مانیتورینگ نشتی
کاهش خطر نشت مواد و آلوده شدن خاک و آبهای زیرزمینی
افزایش ایمنی فرآیندهای صنعتی حساس
4- مخازن کروی
این نوع مخازن معمولا برای نگهداری گازهای فشرده در فشارهای بسیار بالا کاربرد دارند. شکل کروی به دلیل توزیع یکنواخت فشار در سطح باعث افزایش استحکام و کاهش وزن مخزن میشود.
مزایا:
مقاومت بالا نسبت به فشار داخلی
بهینه ترین شکل هندسی از نظر تحمل فشار
استفاده گسترده در صنایع نفت و پتروشیمی
5- مخازن کامپوزیتی
مخازنی که در ساخت آنها از مواد کامپوزیتی مانند فیبرکربن و رزینها استفاده میشود. این مخازن وزن کمتری دارند و نسبت استحکام به وزن بالاتری نسبت به فلزات دارند.
کاربردها:
ذخیرهسازی و انتقال گاز هیدروژن و سوختهای آینده
استفاده در حمل و نقل هوایی و زمینی که وزن پایین اهمیت دارد
قابلیت ساخت اشکال پیچیده و سفارشی
طراحی و ساخت مخازن تحت فشار
مواد استفاده شده
انتخاب مواد برای ساخت مخازن تحت فشار یکی از مهمترین مراحل طراحی است که باید بر اساس شرایط کاری مخزن صورت گیرد. عوامل تعیینکننده در انتخاب ماده شامل نوع سیال، دما، فشار کاری، شرایط محیطی و ملاحظات اقتصادی هستند.
فولاد کربنی
رایجترین ماده برای ساخت مخازن تحت فشار است. فولادهای کربنی به دلیل استحکام بالا، قابلیت جوشکاری خوب و هزینه مناسب، انتخاب غالب در صنایع مختلف هستند. انواع فولادهای خاص مانند فولادهای با ترکیب شیمیایی مقاوم به خوردگی نیز در شرایط ویژه استفاده میشوند.
فولاد ضدزنگ (استنلس استیل)
مناسب برای کاربردهایی که نیاز به مقاومت به خوردگی بالا دارند، مانند مخازن حمل مواد خورنده یا مواد غذایی. فولادهای ضدزنگ مختلفی با ترکیبات متفاوت (304،316 و …) برای مقاومت در برابر انواع محیطها وجود دارند.
آلومینیوم
وزن کمتر و مقاومت خوب در برابر خوردگی از مزایای آلومینیوم است. این فلز در ساخت مخازنی که وزن اهمیت ویژهای دارد کاربرد دارد اما محدودیتهایی در تحمل فشار بالا دارد.
مواد کامپوزیت
در ساخت مخازن پیشرفته که نیاز به وزن بسیار پایین و مقاومت بالا دارند، از مواد کامپوزیتی استفاده میشود. این مواد نسبت به خوردگی بسیار مقاوم بوده ولی برای نقاط اتصال و اتصالات باید طراحی دقیق انجام شود.
فاکتورهای طراحی
طراحی مخازن تحت فشار مستلزم در نظر گرفتن پارامترهای متعددی است که در ادامه به مهمترین آنها اشاره میکنیم:
حداکثر فشار عملیاتی (Maximum Operating Pressure)
مقداری است که مخزن قرار است در حین بهرهبرداری در مقابل آن مقاومت کند. این فشار تعیینکننده ضخامت دیوارهها و انتخاب ماده است. معمولاً حداکثر فشار کاری کمتر از فشار شکست ماده در نظر گرفته میشود و ضریب ایمنی در طراحی لحاظ میشود.
دمای کاری (Operating Temperature)
مواد مختلف رفتار متفاوتی در برابر گرما دارند. دمای بالا میتواند استحکام مواد را کاهش دهد و هنگام طراحی باید تغییرات خواص مواد با دما پرداخت شود.
نوع سیال (Fluid Type)
سیالاتی مانند گازها و مایعات خورنده، سمی، یا قابل اشتعال شرایط متفاوتی را بر مخزن تحمیل میکنند. به همین دلیل لازم است خواص شیمیایی سیال برای انتخاب مواد و طراحی سیستم کنترل نشت بررسی شود.
شرایط محیطی (Environmental Conditions)
شرایطی مانند رطوبت، دماهای محیطی، وجود مواد خورنده یا خاکی، فشار محیط و زلزله نیز بر طراحی و جانمایی مخازن موثر است.
اندازه و شکل هندسی
حجم و ابعاد مخزن تاثیر مستقیمی بر مقدار مواد مصرفی، وزن کلی و هزینه ساخت دارند. شکل هندسی نیز با توجه به کاربرد و محدودیت فضای نصب انتخاب میشود.
ضریب ایمنی (Safety Factor)
با توجه به اهمیت ایمنی، در طراحی مخازن تحت فشار ضرایبی جهت پاسخ به شرایط غیر منتظره مانند افزایش فشار ناگهانی، نقص مواد یا شرایط محیطی غیر عادی در نظر گرفته میشود.
فرآیند ساخت
فرایند ساخت مخازن تحت فشار شامل مراحل متعددی است:
برش ورقها
مواد اولیه بر اساس طرحهای مهندسی به اندازههای دقیق بریده میشوند.
شکل دهی (Forming)
ورقها به شکلهای مورد نیاز مانند استوانه، کروی یا سایر شکلها خمکاری میشوند.
جوشکاری (Welding)
قطعات فرم گرفته به هم متصل میشوند. کیفیت جوشکاری بسیار حیاتی است چون محل جوشها نقاط ضعف احتمالی هستند.
بازرسی و تست غیرمخرب (NDT)
پس از جوشکاری، با روشهایی مانند رادیوگرافی، التراسونیک، تست مغناطیسی و بازرسی چشمی جوشها بررسی میشوند.
آزمون هیدرواستاتیک (Hydrostatic Test)
مخزن تا فشار معینی با آب پر شده و تست میشود تا نشتی و مقاومت آن تایید گردد.
پوشش دهی و رنگ آمیزی
برای جلوگیری از خوردگی و آسیبهای محیطی، مخزن با پوششهای حفاظتی مخصوص رنگ میشود.
نصب لوازم جانبی
مانند شیرآلات، مانومتر، دریچه تخلیه و سیستمهای ایمنی نصب میشود.
ایمنی در مخازن تحت فشار
مخازن تحت فشار به دلیل ذخیره سیالات با فشار بالا میتوانند خطرات متعددی را شامل شوند که در صورت عدم رعایت اصول ایمنی منجر به حادثههای جدی میگردد:
نشتی (Leakage)
در صورت بروز نشتی ممکن است سیال خارج شود و موجب آلودگی محیط، آتشسوزی یا انفجار گردد.
انفجار (Explosion)
افزایش فشار بیش از حد تحمل مخزن، نقص در سیستم ایمنی یا شرایط محیطی ناخواسته میتواند منجر به انفجار شود.
آتشسوزی (Fire)
در مخازن حاوی مواد قابل اشتعال، حادثه آتشسوزی اطلاعات و تجهیزات را به شدت تهدید میکند.
فرسودگی و خوردگی
خوردگی درونی یا بیرونی دیوارهها باعث کاهش استحکام و احتمال شکست فاجعه آمیز میشود.
شکست مکانیکی (Mechanical failure)
عیوب جوشکاری، فشارهای دینامیکی، و ارتعاشات میتوانند باعث ایجاد ترک و شکست شوند.
اقدامات ایمنی
نصب سیستمهای ایمنی
استفاده از شیرهای اطمینان (Safety Relief Valves) برای جلوگیری از افزایش بیش از حد فشار، مانومتر برای نمایش دقیق فشار، و سیستمهای هشدار دهنده.
بازرسیهای دورهای
انجام بازرسیهای منظم شامل آزمایشهای غیرمخرب، بررسی وضعیت پوششها و اندازهگیری ضخامت دیوارهها.
نگهداری مناسب
برنامهریزی تعمیرات پیشگیرانه و حفظ شرایط استاندارد نگهداری جهت جلوگیری از خوردگی و آسیب مکانیکی.
آموزش کارکنان
آموزش پرسنل در زمینه روشهای ایمنی، مدیریت شرایط اضطراری و روشهای استفاده صحیح رساندن به کاهش ریسک کمک میکند.
طراحی با رعایت استانداردها
رعایت استانداردهای بینالمللی و ملی، مانند ASME Boiler and Pressure Vessel Code، API 650 و استانداردهای مرتبط امنیت و دوام مخازن را تضمین میکند.
سیستمهای مانیتورینگ
سیستمهای هوشمند برای پایش فشار، دما و نشتی به منظور شناسایی به موقع مشکلات احتمالی.
کاربردهای مخازن تحت فشار
مخازن تحت فشار در صنایع مختلف کاربرد فراوانی دارند که در ادامه به مهمترین آنها اشاره میشود:
ذخیره گازهای صنعتی و شیمیایی
گازهای هیدروژن، نیتروژن، اکسیژن، و گازهای خاص صنعتی در مخازن تحت فشار ذخیره میشوند تا در عملیات تولید و انتقال مورد استفاده قرار گیرند.
سیستمهای آب و فاضلاب
مخازن تحت فشار در تنظیم و ذخیره فشار آب، هوادهی به فاضلاب و تزریق مواد شیمیایی کاربرد دارند.
ذخیره سوخت در صنایع نفت و گاز
نگهداری نفت، گاز مایع (LPG) و سایر سوختهای مایع تحت شرایط فشار و دما کنترل شده از ویژگیهای حیاتی این مخازن است.
صنایع نیروی برق
استفاده در نیروگاهها برای ذخیره مواد مختلف، تنظیم فشار آب دیگهای بخار و ذخیره گازهای خنک کننده.
صنایع دارویی و غذایی
نگهداری مواد حساس به آلودگی با فشار کنترل شده و شرایط خاص محیطی.
سیستم های هیدرولیک و پنوماتیک
مخازن تحت فشار به عنوان مخزن ذخیره انرژی در این سیستمها استفاده میشوند.
نتیجه گیری
مخازن تحت فشار نقش حیاتی در صنایع مختلف ایفا میکنند. طراحی صحیح و بهینه این مخازن، انتخاب مواد مناسب بر اساس کاربرد و شرایط کاری، و رعایت نکات ایمنی از جمله موارد کلیدی برای عملکرد مطمئن و ایمن آنها به حساب می آید.
با توجه به شرایط متغیر دما و فشار، استفاده از استانداردهای بهروز و تکنولوژیهای نوین ساخت میتواند به بهینه سازی فرآیندها و افزایش ایمنی کمک کند.
آموزش مداوم پرسنل و بازرسیهای دورهای نیز از اصول اساسی در حفظ سلامت و کارکرد بهینه مخازن تحت فشار است.